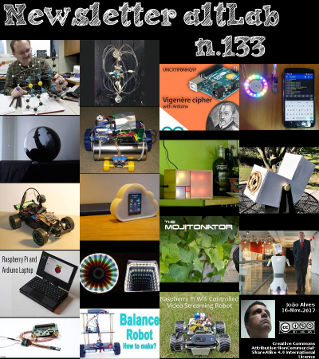
Faz hoje anos que nascia, em 1717, Jean le Rond d’Alembert. Este matemático francês ficou conhecido pelo seu trabalho em vários campos da matemática aplicada, em particular o da dinâmica. Em 1743 publicou seu “Traité de Dynamique”, no qual aplica a terceira lei do movimento de Newton, em que a lei de Newton não só é válida para os corpos fixos, mas também para os corpos em movimento livre. D’Alembert também escreveu sobre a dinâmica dos fluidos, a teoria dos ventos, as propriedades das cordas vibratórias e experiências conduzidas sobre as propriedades do som. A sua inovação puramente matemática mais significativa foi sua invenção e desenvolvimento da teoria das equações diferenciais parciais.
Faz também anos hoje que nascia, em 1835, Eugenio Beltrami. Este Matemático e físico matemático italiano ficou conhecido pelos seus conceitos de geometria não euclidiana. Em 1865, ele publicou um artigo sobre como elementos de linha nas superfícies de curvatura constante poderiam ser representados por expressões lineares. A sua abordagem ofereceu uma nova representação da geometria de curvatura constante que era consistente com a teoria euclidiana. Beltrami estudou elasticidade, teoria das ondas, óptica, termodinâmica e a teoria do potencial. Foi o primeiro a explorar os conceitos de hiperespaço e tempo como uma quarta dimensão. As suas investigações na condução de calor levaram a equações diferenciais parciais lineares. Alguns dos últimos trabalhos de Beltrami estavam numa interpretação mecânica das equações de Maxwell.
Por fim, faz anos hoje que nascia, em 1841, Jules Violle. Este físico francês nascido em Langres, fez a primeira determinação de altitude da constante solar (em 1875, no Mont Blanc nos Alpes franceses e suíços). Ele também determinou os pontos de fusão de paládio, platina e ouro. Violle também estava interessado na teoria dos geysers, na origem do granizo e na exploração atmosférica através de amostragens por balão. Para radiação de alta temperatura, ele propôs uma unidade fotométrica, a violle ou o padrão de Violle (1881). Seu actinômetro é uma forma de pirheliômetro, um dispositivo para medir a intensidade da luz solar. Foi modificado a partir da invenção de John Herschel de 1825. Ele consiste em duas esferas concêntricas vazias contendo água entre elas. A luz do sol passa através de uma abertura e cai sobre uma lâmpada do termómetro na esfera interna oca.
Na semana que passou ficámos a saber que a Waymo agora está a testar os seus carros autónomos na via pública sem ninguém ao volante. Os testes também não estão limitados a uma ou duas rotas; A área de teste onde os ensaios verdadeiramente sem condutor estão a ser realizados é em Chandler, Arizona (parte da área metropolitana de Phoenix), e os carros podem ir a qualquer lugar dentro desse espaço definido. É difícil subestimar a importância deste marco: a Waymo está a operar em autonomia de nível 4, partilhando estradas públicas com carros e pedestres humanos, sem que ninguém no volante possa assumir o controlo, caso as coisas não funcionem como planeado.
Também esta semana uma equipa médica alemã procedeu à troca de cerca de 80 porcento da pele de uma criança de sete anos. Esta medida foi necessária para salvar a vida da criança que tinha uma patologia rara que lhe provocava feridas e bolhas expostas. Uma unidade de queimados tentou, sem sucesso, um tratamento convencional. Os médicos retiraram uma pequena amostra de pele de um dos poucos lugares no corpo da criança, que não estava afectada, e enviou para o prof. De Luca. A sua equipa no centro usou um vírus para inserir nas células da pele uma cópia correta de um gene chamado LAMB3; A própria cópia defeituosa do menino causou sua epidermólise bolhosa. De Luca e seus colegas cresceram as células da pele sobre estruturas artificiais no seu laboratório para formar grandes pedaços. Estes foram posteiormente aplicados em duas cirurgias na criança.
Ainda esta semana, Linus Torvalds anunciou a versão 4.14 do Kernel Linux. Esta versão tem um significado especial por ser de suporte longo (LTS). Apelidado de “Fearless Coyote”, esta versão traz como novidades uma maior capacidade de endereçamento de memória na arquitectura x86_64, melhorias VEGA, suporte para compressão zstd adicionado, AMD Secure Memory Encryption em CPUs EPYC, novo driver wifi realtek, melhorias nos filesystems F2FS para Android e Btrfs, EXT4, XFS, etc.
Na Newsletter desta semana apresentamos diversos projetos de maker assim como dois modelos 3D que poderão ser úteis. É apresentado também o livro “Don’t Panic: Mobile Developer’s Guide to The Galaxy, 17th Edition”.
Esta Newsletter encontra-se mais uma vez disponível no sistema documenta do altLab. Todas as Newsletters encontram-se indexadas no link.